Motor Control
The electric motor is a device that converts electrical energy into mechanical energy, it uses electricity and magnetic field to produce torque to turn the rotor and hence give mechanical work.
Depending upon the application where the motor is used, the motors are controlled by computerized control systems, like solid-state logic controls, or programmable logic controllers (PLCs) to control and manage their torque, speeds, the work or energy delivered. Motor controllers can have many features of controlling a motor that may include but are not limited to starting, stopping, over-current protection, overload protection, reversing, speed changing, jogging, p lugging as well as sequence control. Motor Controllers range from simple to complex and can provide control for one motor or groups of motors.
Motors are broadly classified into two categories; AC Motors and DC Motors, based on the source of electrical energy used.
DC – Motor Types: Series, Shunt/Parallel and Compound based on the way the field coils and armature coil circuits are wired. Other types of DC Motors are the Permanent Magnet (PMDC) Motors and Separately Excited Motors.
AC – Motor Types: AC Induction Motors (also known as asynchronous motor) and Synchronous Motors. They are further classified by their applications like single phase, three phase, Squirrel Cage Induction, Dual Voltage etc.
Read moreStay informed
Keep up to date on the latest information and exclusive offers!
Subscribe now
Thanks for subscribing
Well done! You are now part of an elite group who receive the latest info on products, technologies and applications straight to your inbox.
Building blocks of motor control
Roll over the icons below for more information
Motor Controls
Sensors
Motor Dev Kits
Semiconductors - Ics
Semiconductors - Discretes
Motor Start/Run/Line Filters
Brushed DC (BDC)
Brushed DC (BDC) motors get their name from the "brushes" used for commutation. Brushed DC motors are used frequently in household appliances and in automobiles. They also maintain a strong industrial niche because of the ability to alter the torque to speed ratio exclusive to brushed motors. BDC are easy to control because speed and torque are proportional to the applied voltage / current.
A brushed DC motor is made up of 4 basic components; the stator, the rotor (or armature), brushes, and commutator. The rotor, also known as the armature made up of one or more windings. When these windings are energized they produce a magnetic field. The magnetic poles of this rotor field will be attracted to the opposite poles generated by the stator, causing the rotor to turn. As the motor turns, the windings are constantly being energized in a different sequence so that the magnetic poles generated by the rotor do not overrun the poles generated in the stator. This switching of the field in the rotor windings is called Commutation. The rotation’s direction, clockwise and/or counter clockwise, can be reversed easily by reversing the polarity of the brushes, i.e., reversing the leads on the battery.
There are four types of BDC motors. Permanent Magnet Brush DC Motor, the shunt-wound brushed DC motor, series-wound DC motor and fourth is the compound-wound brushed DC motor which is a combination of both the shunt and series wound brushed DC motors.
Related product categories
Brushless DC (BLDC)
The Brushless DC (BLDC) motor is also referred to as an electronically commutated motor. There are no brushes on the rotor and commutation is performed electronically at certain rotor positions. A BLDC motor is a Permanent Magnet Synchronous Motor with unique back EMF waveform that allows them to behave similarly to a brushed DC motor. BLDC motor does not directly operate off a DC voltage source. However, the basic principle of operation is similar to a DC motor.
A Brushless DC Motor has a rotor with permanent magnets and a stator with windings, A BLDC motor is essentially a DC motor turned inside out. Brushes and commutator have been eliminated and the windings are connected to the control electronics. Control electronics replace the function of the commutator and energize the proper winding, Windings are energized in a pattern which rotates around the stator, the energized stator winding leads the rotor magnet and switches just as the rotor aligns with the stator.
The Brushless DC motor is the ideal choice for applications that require high reliability, high efficiency, and high power-to-volume ratio. Generally speaking, a BLDC motor is considered to be a high performance motor that is capable of providing large amounts of torque over a vast speed range.
Related product categories
Induction-motor-ac
One of the most common electrical motor used in most applications which is known as Induction Motor. This motor is also called as asynchronous motor because the rotor always turns at a lower speed than the field, making it an asynchronous AC motor. It runs at a speed less than its synchronous speed. AC induction motors are either single-phase or poly-phase. The Single phase power system is widely used as compared to three phase system for domestic purpose, commercial purpose and to some extent in industrial purpose.
The stator of the motor consists of overlapping winding offset. When the primary winding or the stator is connected to AC source, it establishes a rotating magnetic field which rotates at the synchronous speed. The theoretical speed of the rotor in an induction motor depends on the frequency of the AC supply and the number of coils that make up the stator and, with no load on the motor, comes close to the speed of the rotating magnetic field. It turns at a constant speed unless you use a variable-frequency drive.
The biggest advantage of AC induction motors is their sheer simplicity. They have only one moving part, the rotor, which makes them low-cost, quiet, long-lasting, and relatively trouble free. Induction motors can be fairly heavy and bulky because of their coil windings. Three phase IM are widely used in industrial drives, Lifts, Cranes, Driving lathe machine..etc because they are rugged, reliable and economical. Single-phase IM are used extensively for smaller loads, such as household appliances like fans, pumps, mixer, toys, vacuum cleaner, Drilling machines etc.
Related product categories
Permanent-magnet-synchronous-motor
The Permanent Magnet Synchronous Motor (PMSM) is an AC synchronous motor whose field excitation is provided by permanent magnets, and has a sinusoidal back EMF waveform. The PMSM is a cross between an induction motor and brushless DC motor. Like a brushless DC motor, it has a permanent magnet rotor and windings on the stator. However, the stator structure with windings constructed to produce a sinusoidal flux density in the air gap of the machine resembles that of an induction motor. Its power density is higher than induction motors with the same ratings since there is no stator power dedicated to magnetic field production.
With permanent magnets the PMSM can generate torque at zero speed, it requires digitally controlled inverter for operations. PMSM are typically used for high-performance and high-efficiency motor drives. High-performance motor control is characterized by smooth rotation over the entire speed range of the motor, full torque control at zero speed, and fast acceleration and deceleration.
To achieve such control, vector control techniques are used for PMSM. The vector control techniques are usually also referred to as field-oriented control (FOC). The basic idea of the vector control algorithm is to decompose a stator current into a magnetic field-generating part and a torque-generating part. Both components can be controlled separately after decomposition.
Stepper motor
A stepper motor is a brushless DC electric motor that divides a full rotation into a number of equal steps. It rotates a specific incremental distance per each step. The number of steps that are executed controls the degree of rotation of the motor’s shaft.
Stepper motors have some inherent ability to control position, as they have built-in output steps. It can very accurately control how far and how fast the stepper motor will rotate. The number of steps the motor executes is equal to the number of pulse commands given by the controller. A stepper will rotate a distance and at a rate that is proportional to the number and frequency of its pulse commands.
A stepper motor controller can be either open loop or closed loop. The difference between the two is that an open loop system sends a consistent rate of power to the motor, assuming that the rotating field that the rotor follows is consistent. A closed loop system uses feedback to adjust power based on the kind of load the motor is bearing. Most motor applications work with an open loop system, because it is simpler and less expensive.
Stepper motors have several advantages over other types of motors. One of the most impressive is their ability to position very accurately. It can achieve the same target position, revolution after revolution. Standard stepper motors have a step angle accuracy of +/-5%. The error does not accumulate from step to step.
Related product categories
Servo Motor
A servomotor is a rotary actuator or linear actuator that allows for high-response, high-precision control of angular or linear position, velocity and acceleration. As a motor capable of the accurate rotation angle and speed control, it can be used for a variety of equipment. They are used in applications such as robotics, CNC machinery or automated manufacturing and are generally used as a high-performance alternative to the stepper motor.
Servo systems combine a high-performance servo motor with a servo amplifier (drive) to achieve the extremely accurate position, velocity, or torque control. Servos have integrated gears and a shaft that can be precisely controlled. The servo circuitry is built right inside the motor unit and has a positionable shaft, which usually is fitted with a gear. The motor is controlled with an electric signal which determines the amount of movement of the shaft.
In a closed loop control, a rotation detector (encoder) is mounted on the motor and feeds the rotation position/speed of the motor shaft back to the driver. The driver calculates the error of the pulse signal or analog voltage (position command / speed command) from the controller and the feedback signal (current position/speed) and controls the motor rotation so the error becomes zero. The closed loop control method is achieved with a driver, motor and encoder, so the motor can carry out highly accurate positioning operations. In a position control system, a controller inputs the pulse signal, the speed and stop position is then controlled according to the pulse number.
Related product categories
Featured content
Solution guide

Electromagnetic Contactors Explained : An Essential Guide for efficient power control
Explore contactors in this guide! Learn their functionality, applications, key differences from relays, and selection tips to help engineers and maintenance professionals choose the right solution.
How-to
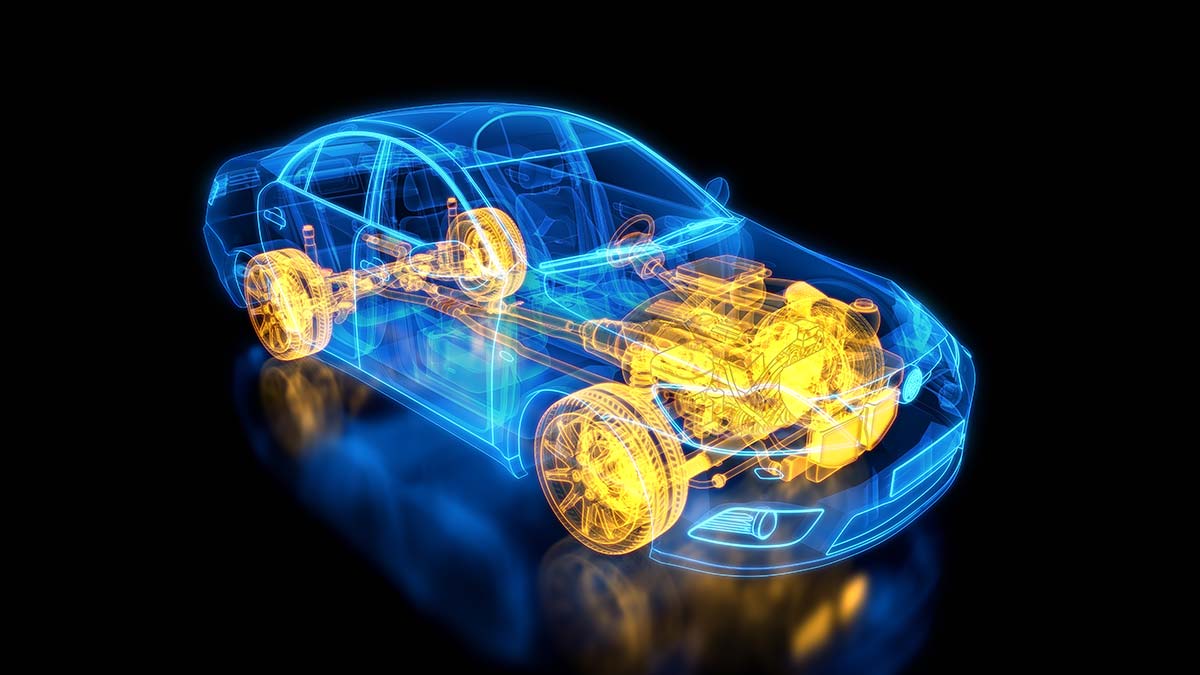
How to fail safe SIL motor control technology
How to ensure safety integrity level (SIL) using Fail- Safe Motor Control Technology.
Blog
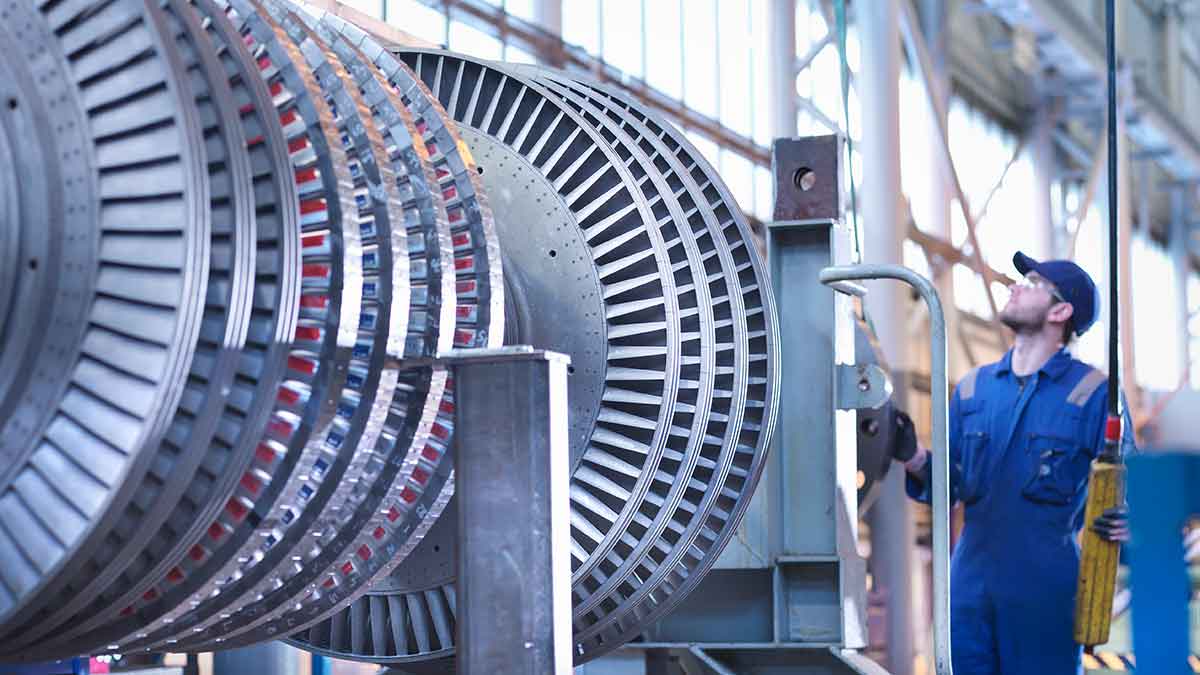
Variable speed drives improve machine efficiency in smart industrial application
This blog provides a comprehensive overview of VSD applications in improving machine efficiency and saving energy from electrical motors in industrial applications.
Article
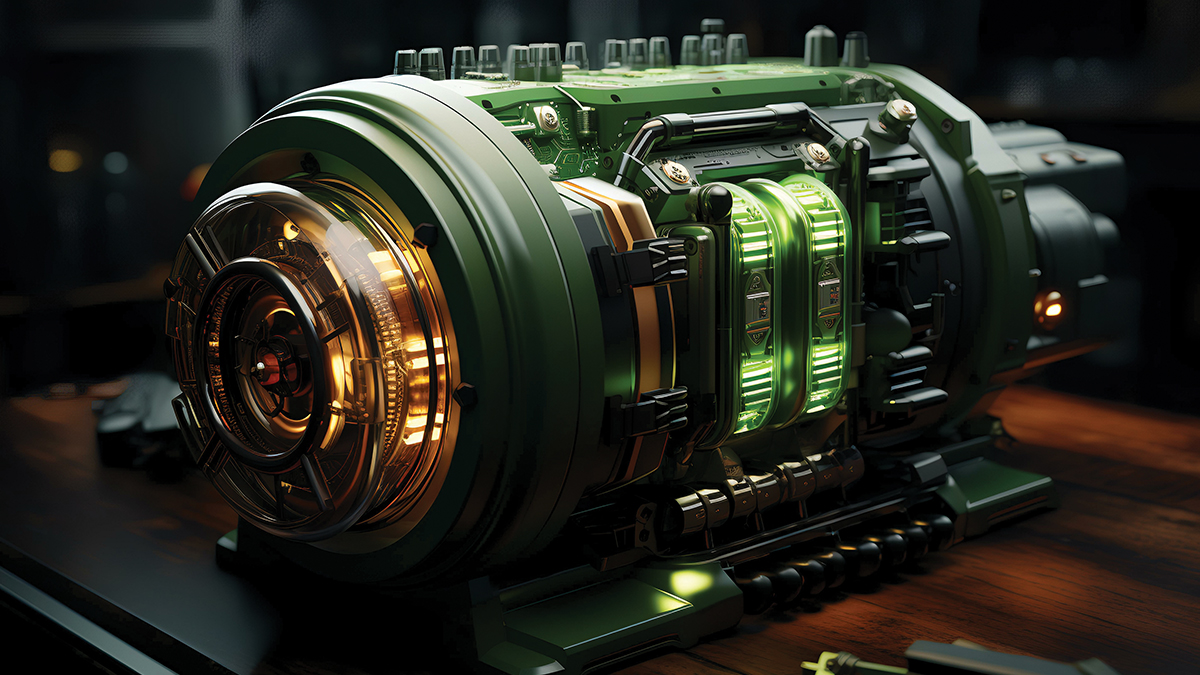
Toshiba: MCU-less Sinusoidal Control of Permanent Magnet Synchronous Motors
Explore MCU-less sinusoidal control for PMSMs, which provides silent, smooth motion in high-end appliances and automation. Unlike BLDC motors, PMSMs require sophisticated sinusoidal commutation. MCUs require substantial optimization. However, recent technologies simplify this process, improving performance and lowering complexit