Variable Speed Drives improve machine efficiency in Industrial Application
Different speeds are now demanded by technology in many applications where electric motors are utilized. Variable Speed Drives (VSD) play an important role in driving efficiency in motor industrial applications during the design stage and on the shop floor. Section 2 of the whitepaper "Smart Solutions for Energy Efficiency" discusses the Energy efficiency of machines with Automation (click here for more details). This blog provides a comprehensive overview of VSD applications in improving machine efficiency and saving energy from electrical motors in industrial applications.
A Rectifier, Intermediate circuit, Inverter, and Control unit are the key components of a VSD unit, as illustrated in figure 1 below. The rectifier changes alternating current (AC) to direct current (DC). In the intermediate circuit, the rectified DC supply is typically conditioned by a combination of inductors and capacitors. The inverter converts the rectified and conditioned DC back into a variable frequency and voltage AC supply. Normally, this is accomplished by generating high-frequency pulse width modulated signal with changing frequency and effective voltage. The control unit supervises the whole operation of the VSD; it monitors and controls the rectifier, intermediate circuit, and inverter to ensure that the right output is delivered in response to an external control signal.
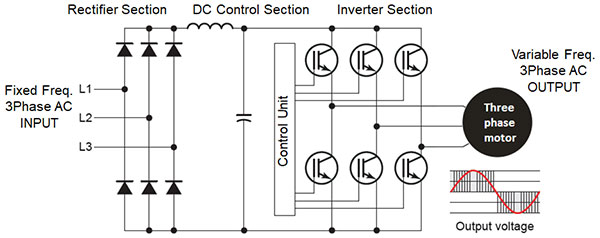
Fig 1: Schematic of a Variable Speed Drive
VSDs application with various loads:
The VSD will be interfaced with a transducer such as a pressure, or flow rate sensor, and programmed to maintain a certain value (set point). They may interface with several transducers, implement interlocks and other control functions, and connect with current computer networks, which provide real-time operational data.
The potential of VSDs to save energy is based on the characteristics of the load being driven. Loads are classified into three types: variable torque, constant torque, and constant power. Variable torque loads are prevalent in centrifugal fans and pumps and provide the largest potential for energy savings. This is because torque changes with speed squared (H1/H2 = (N1/N2)2) and power vary with speed cubed (P1/P2 = (N1/N2)3). And the flow changes according to the change in speed (Q1/Q2 = (N1/N2)).
As shown in the diagram below, Constant torque loads are those in which the torque does not vary with speed, and the power absorbed is directly proportional to the speed, implying that the power consumed is proportional to the useful work done.

Fig 2: (a) Constant Torque Load Profile. (b) Energy Saving from different loads
Conveyors, agitators, crushers, surface winders, positive displacement pumps, and air compressors are typical of constant torque applications. On constant power loads, the power absorbed is constant whilst the torque is inversely proportional to the speed.
Variable-speed fan control can be used in a wide range of applications, including most kinds of ventilation systems, air extract systems, industrial cooling, and boiler combustion-air control systems.
The curve in figure 3 below indicates that using a VSD to regulate the flow rate from a pump rather than a conventional throttle control can result in significant power and cost savings. Where the dotted line represents the power input to a fixed-speed motor and the solid line represents the power input to a variable-speed drive (VSD). The shaded region reflects the amount of energy saved by employing a VSD for a given flow.
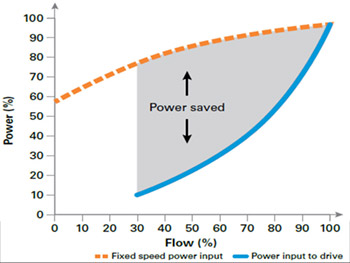
Fig 3: Pump power-saving- throttle valve vs. speed reduction
VSDs are supplied in a wide range of sizes from 0.18kW through to several MW and may be optimizeed to suit particular applications. VSDs are typically 92–95% efficient with 5–8% losses being due to additional heat dissipation caused by the high–frequency electrical switching and the additional power required by the electronic components. The losses are usually more than compensated for by the savings at the motor.
Newark has partnered with many different suppliers catering to a wide range of Variable Frequency Drives products, and solutions portfolios, such as Motor Control, Motor Starters, Electric Motors, Motor Protection Accessories, Motor Drives
Stay informed
Keep up to date on the latest information and exclusive offers!
Subscribe now
Thanks for subscribing
Well done! You are now part of an elite group who receive the latest info on products, technologies and applications straight to your inbox.